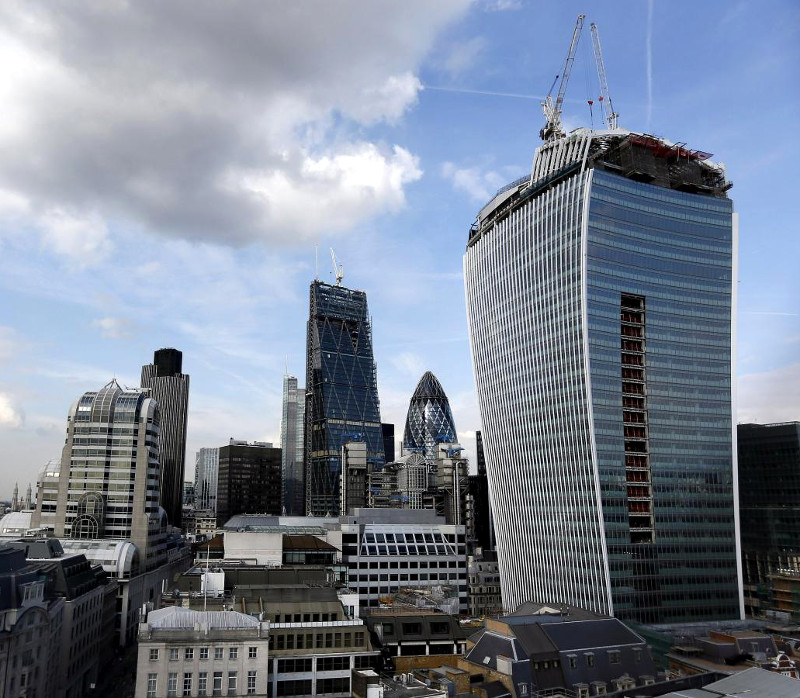
Have you ever come across a situation where something, utterly negligible and minor, had become a cause for a major disruption or even an accident? Such as a small crack in an underground water pipe, dripping inconspicuously for a couple of years, and eventually causing a landslide after accumulating a critical mass of water? Or a seemingly common glass building capable of focusing the sunlight so that it melts the bodywork of cars parked nearby?
If so, chances are high that you observed an example of the Dropped Washer effect. Named after a Boeing 737 accident in Okinawa, Japan, the dropped washer effect describes large-scale adverse events that happened because of the cause of an incomparably lower significance. The unfortunate Boeing ended up burning out completely because of a missing slat mechanism washer, 0.625 inches wide, that the engineering crew forgot to replace after the aircraft’s last service.
One characteristic of the potential dropped-washer features that makes them particularly naughty is their zero perceived value for the business. Offering no added opportunities and presenting no apparent risks for the product, they often do not even exist in the minds of the product stakeholders. This important peculiarity makes it all too easy for them to slip every safety measure employed in modern production flows – from risk assessment to quality control.
Happily, in many cases there are techniques that can help increase our chances of spotting and eliminating the dropped washers from our projects.
Check out my new paper here.
Picture credit: Reuters